CASE STUDIES
Inspiring Success Stories of Geosynthetics and GeoHazard Mitigation projects of TechFab India

Filters
filter by industry
filter by application
filter by product categories
EXCELLENCE THROUGH INNOVATION
Case Studies
Discover the limitless possibilities of Geosynthetics and GeoHazard Mitigation products through these inspiring case studies. From diverse applications to groundbreaking innovations, experience the advantages and benefits of using these products with greater confidence. Join us in promoting their inclusion in industry standards and guidelines.
TALK TO THE BEST
Speak to a TFI Expert
Contact our Technical Expert to learn more about our offerings. Our experts are ready to assist you for your specific project requirement. Get in touch now!
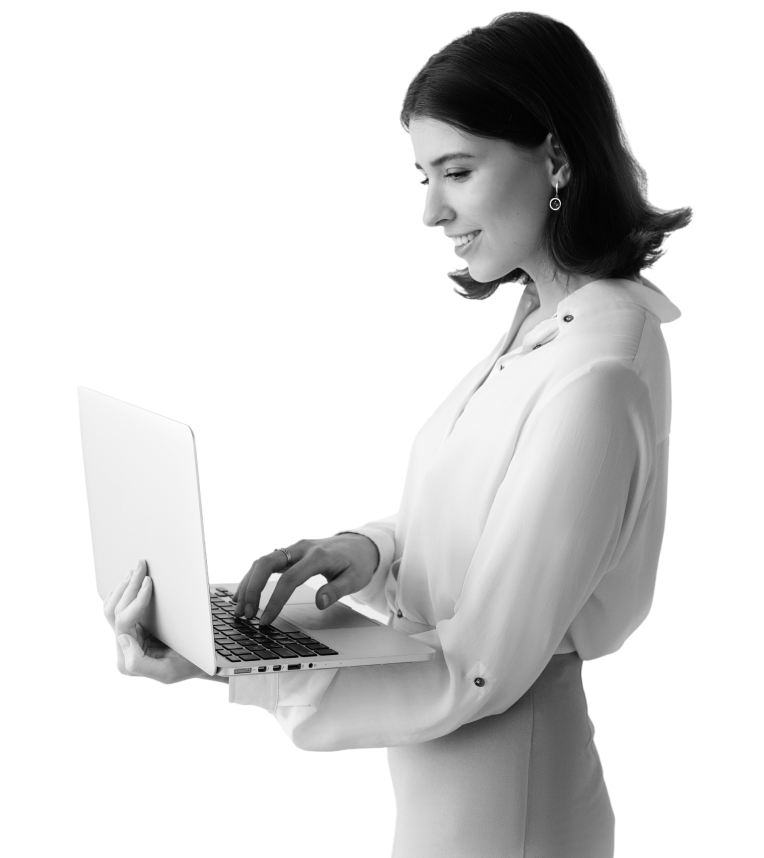